Dans le secteur industriel, un plan de maintenance va bien au-delà de simples interventions ponctuelles. C’est un système stratégique et intégré qui repose sur une approche méthodique pour garantir la durabilité des équipements tout en optimisant les coûts et en améliorant la productivité globale. Il s’agit d’un document qui comprend l’ensemble des actions nécessaires à la gestion proactive des équipements industriels afin de minimiser les risques de défaillances non planifiées, et ainsi assurer une production fluide et continue.
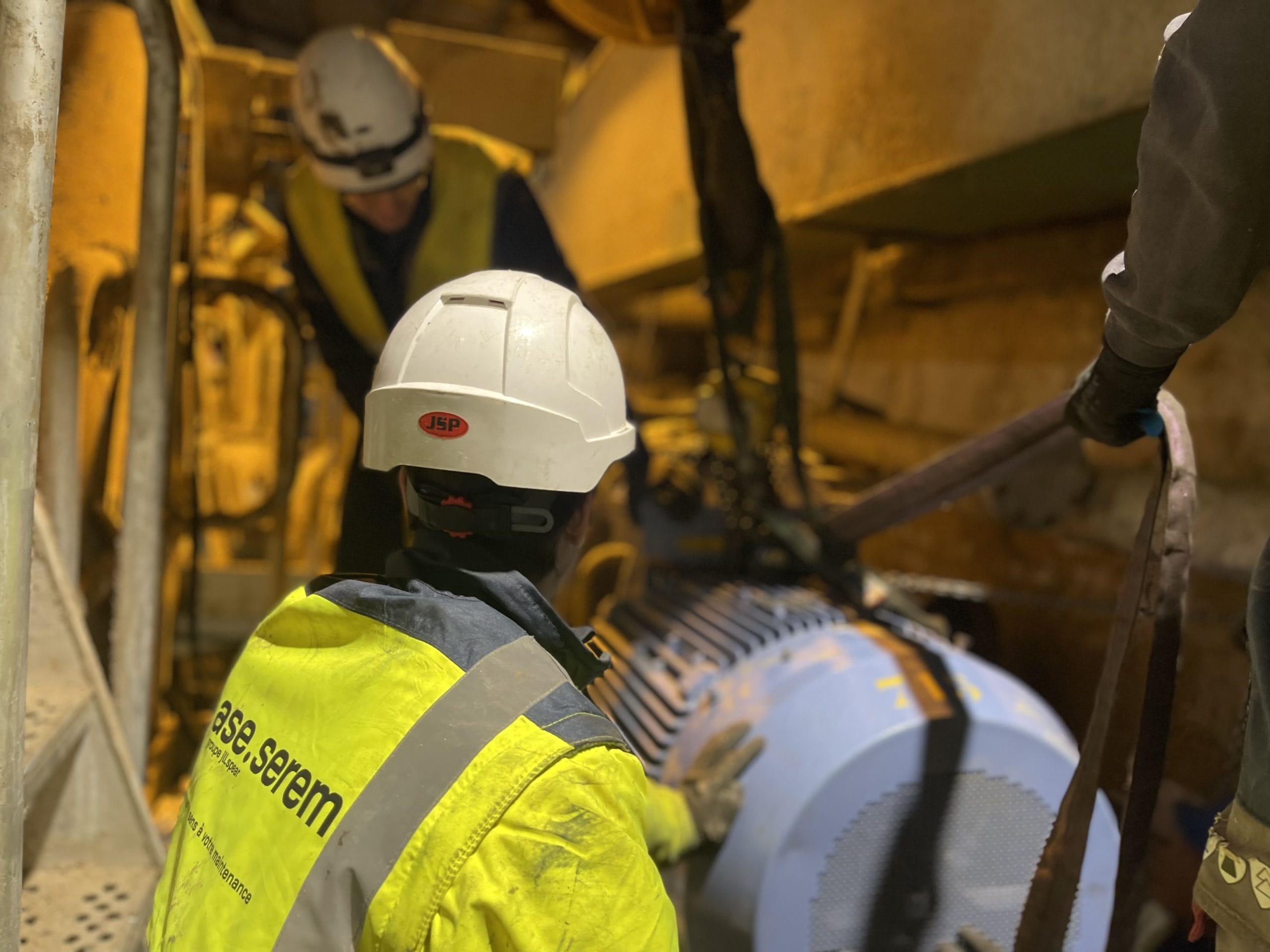
Sommaire
Les objectifs du plan de maintenance industrielle
Le plan de maintenance n’est pas qu’une simple liste d’interventions ; il s’agit d’une démarche structurée visant à atteindre des objectifs clairs et mesurables :
- Prolongation de la durée de vie des équipements : En traitant les machines avant qu’elles ne présentent des défaillances majeures, le plan de maintenance permet d’optimiser la durée de vie des équipements. En fonction de l’intensité de l’utilisation, un plan détaillé permettra d’éviter l’usure prématurée et de minimiser les coûts de remplacement.
- Réduction des coûts de maintenance : L’anticipation permet de réaliser une maintenance conditionnelle ou prédictive, réduisant ainsi les coûts par rapport à une maintenance uniquement corrective. Grâce à des outils comme la GMAO, les équipes de maintenance peuvent détecter les signes avant-coureurs de panne et intervenir en temps opportun.
- Amélioration de la sécurité des équipements : L’un des objectifs sous-jacents du plan est de garantir la sécurité des opérateurs en assurant un suivi constant de l’état des machines et en réagissant rapidement en cas de défaillance technique qui pourrait affecter la sécurité sur site.
À lire aussi 💡Quels sont les 5 types de maintenance ?
Les étapes de mise en place d’un plan de maintenance industrielle efficace
Un plan de maintenance bien structuré se construit en plusieurs étapes rigoureuses, chacune nécessitant des outils et des approches spécifiques pour garantir la réussite du processus.
Inventaire détaillé et classification des équipements
La première étape consiste à réaliser un inventaire précis de l’ensemble des équipements industriels. Cela ne se limite pas à une simple liste, mais comprend une analyse détaillée de :
- Les spécifications techniques : Type de machine, marque, modèle, année de fabrication.
- Les performances requises : Températures de fonctionnement, cycles de production, limites de charge, etc.
- L’historique des interventions : Ces informations sont essentielles pour détecter les patterns de défaillance et adapter les programmes de maintenance.
L’analyse de ces informations permet d’établir des priorités d’intervention, en fonction de la criticité des équipements et de leur impact potentiel sur la production.
Évaluation des risques et analyse de défaillance
Chaque équipement est susceptible de tomber en panne, mais toutes les pannes n’ont pas le même impact. Un audit de maintenance approfondi doit être réalisé pour identifier les facteurs de performance et les taux de défaillance des équipements. Cette analyse de risques inclut :
- L’identification des modes de défaillance : les types de pannes les plus fréquentes, comme les pannes mécaniques, électriques, ou liées à la sécurité des machines.
- L’impact potentiel d’une panne sur la production : la durée d’indisponibilité, les pertes économiques, et l’impact sur la qualité de production.
L’objectif est de prioriser les actions de maintenance sur les équipements ayant le plus grand impact sur la chaîne de production.
Définition des stratégies de maintenance adaptées
Le plan de maintenance doit inclure des stratégies adaptées à chaque type d’équipement, et ce choix repose sur les données recueillies lors des étapes précédentes. Les stratégies principales sont :
- Maintenance préventive : Interventions programmées régulièrement (par exemple, selon un calendrier fixe ou basé sur des heures de fonctionnement). Cela comprend l’inspection des composants critiques, la lubrification, le nettoyage, le remplacement des pièces d’usure, etc. Les procédures de maintenance préventive doivent être standardisées et rigoureusement suivies.
- Maintenance corrective : Interventions sur pannes détectées, nécessitant une réparation rapide. Cette maintenance doit être gérée pour ne pas interrompre la production de manière excessive.
- Maintenance prédictive : Utilisation de la maintenance conditionnelle basée sur des données en temps réel recueillies via des capteurs IoT, l’analyse vibratoire, ou la thermographie. La maintenance prédictive repose sur des techniques telles que la modélisation des défaillances et les algorithmes d’intelligence artificielle pour anticiper les pannes avant leur apparition.
Les outils de GMAO sont essentiels pour gérer ces différentes stratégies, en automatisant la planification des interventions et en collectant des données sur l’état des équipements en temps réel.
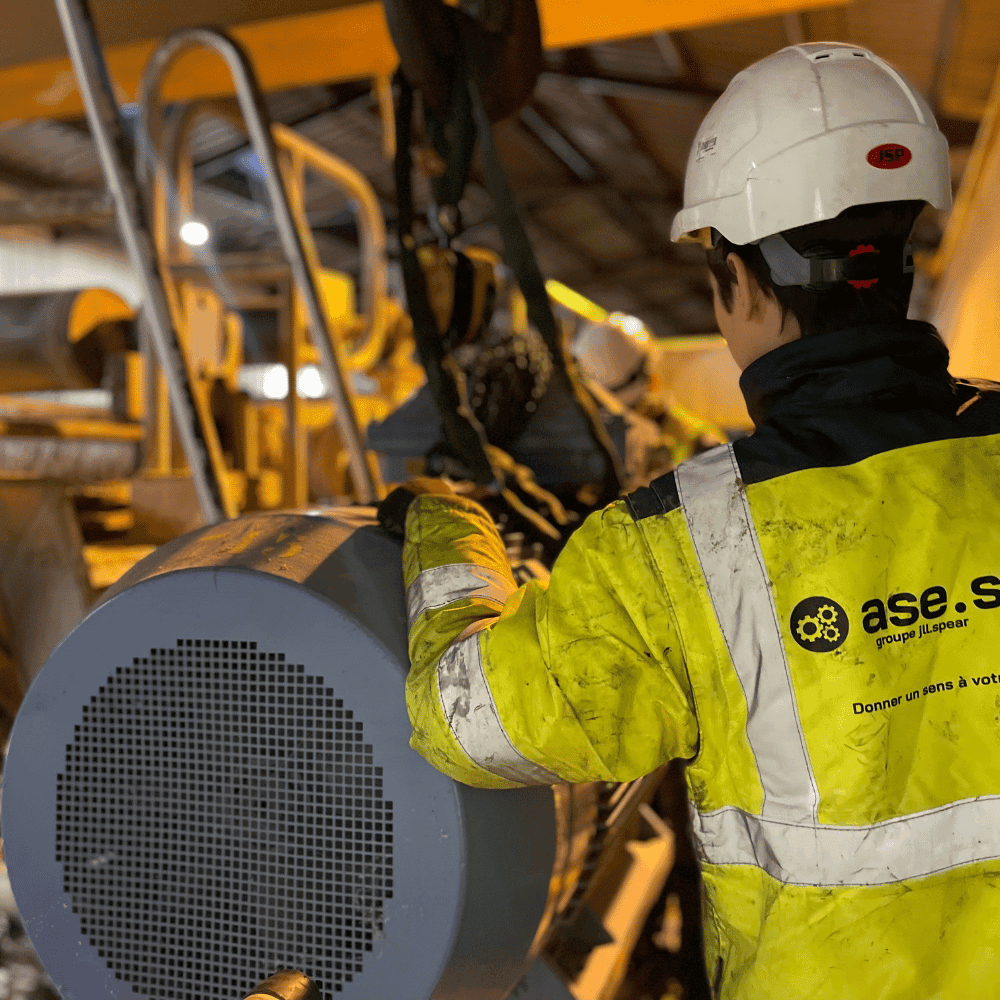
Mise en place d’indicateurs clés de performance (KPI)
Les KPI de maintenance permettent de suivre l’efficacité des actions de maintenance et d’ajuster les stratégies en fonction des résultats obtenus. Parmi les indicateurs essentiels, on retrouve :
- Le taux de disponibilité des équipements.
- Le temps moyen entre les pannes (MTBF – Mean Time Between Failures).
- Le temps moyen de réparation (MTTR – Mean Time To Repair).
- Le coût total de maintenance, incluant les coûts de la main-d’œuvre, des pièces de rechange, et des outils de maintenance.
- L’impact environnemental des opérations de maintenance, notamment en termes de gestion des déchets, de consommation d’énergie et d’émissions.
Suivi et révision continue
Un plan de maintenance efficace n’est pas statique. Il doit être réévalué régulièrement à travers des revues de performance et des audits périodiques. Cette révision doit inclure :
- L’analyse des résultats des KPI de maintenance.
- La mise à jour des procédures de maintenance en fonction des nouvelles normes ou des améliorations techniques.
- L’intégration de nouvelles technologies de maintenance prédictive et de logiciels de GMAO pour affiner les prévisions et optimiser les interventions.
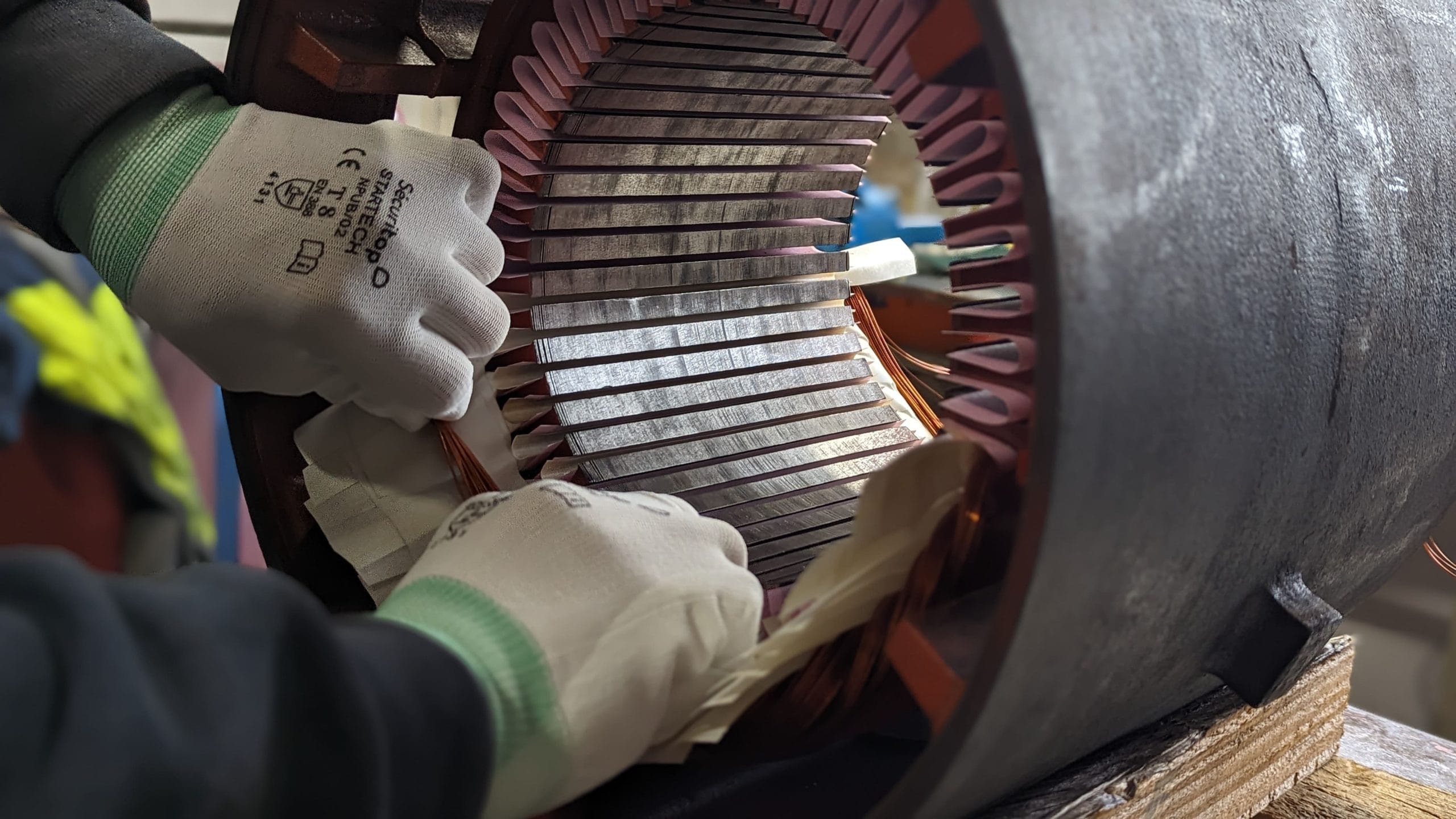
Outils de facilitation : GMAO et technologies avancées
La mise en œuvre d’un plan de maintenance nécessite des outils efficaces pour automatiser et optimiser les processus. L’un des outils les plus puissants est la GMAO (Gestion de la Maintenance Assistée par Ordinateur), qui permet de :
- Automatiser la planification des interventions.
- Suivre l’historique des interventions et des pièces de rechange.
- Collecter et analyser des données issues de capteurs IoT et d’autres dispositifs de surveillance, pour prédire les pannes et ajuster les actions de maintenance en conséquence.
De plus, l’utilisation de drones industriels et de technologies telles que l’analyse vibratoire, la thermographie et l’intégration des systèmes IoT dans la stratégie de maintenance peut fournir des insights précieux pour anticiper les pannes avant qu’elles ne se produisent.
Conclusion.
Un plan de maintenance bien conçu permet non seulement d’assurer la fiabilité des équipements industriels mais aussi de maîtriser les coûts de maintenance à long terme. L’anticipation des pannes, la planification minutieuse des interventions, l’intégration de technologies avancées et la gestion continue de la performance sont les clés pour maximiser l’efficacité opérationnelle et garantir la sécurité des installations.
Le véritable défi est de ne pas considérer la maintenance comme une activité réactive, mais bien comme un levier stratégique pour optimiser la production, la sécurité, et l’impact environnemental des opérations industrielles.
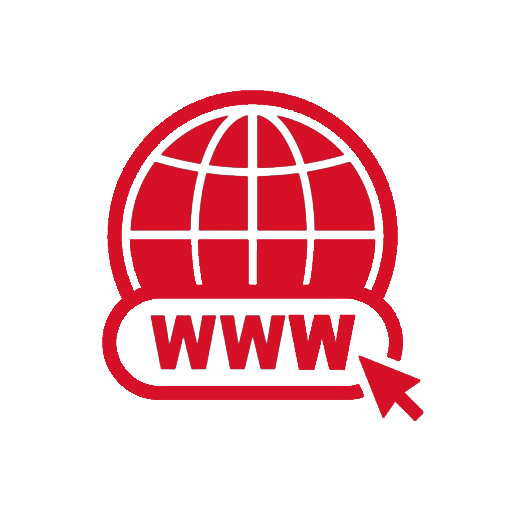
Découvrez notre offre de maintenance industrielle.
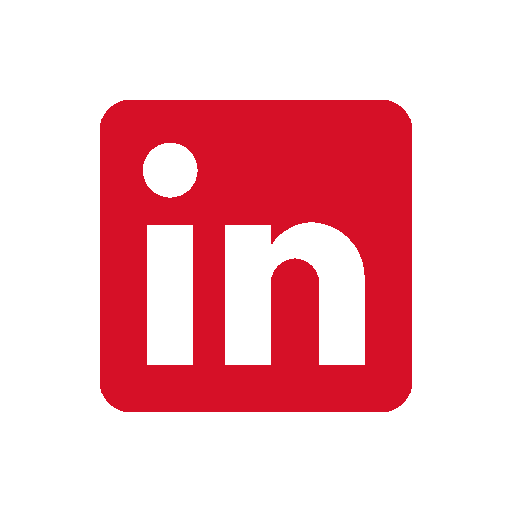
Découvrez l’actualité de notre atelier au quotidien via notre page LinkedIn !